Choosing the Best Defoamers for Your Manufacturing Line
Choosing the Best Defoamers for Your Manufacturing Line
Blog Article
How Defoamers Improve Effectiveness in Manufacturing and Production
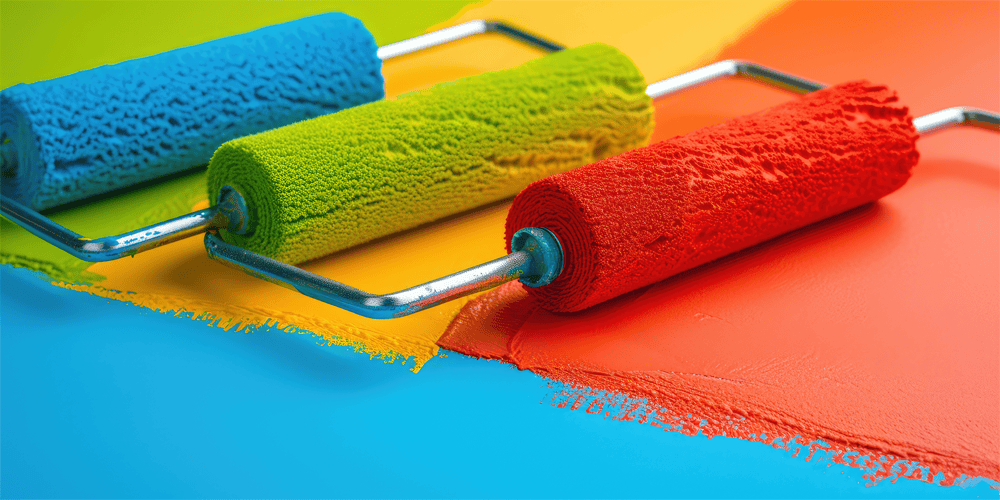
Comprehending Defoamers
Defoamers play a critical role in various manufacturing procedures by effectively combating the development of foam, which can interrupt operations and impact product top quality. Foam can occur in numerous contexts, such as during mixing, home heating, or chemical responses, potentially leading to ineffectiveness and incongruities in products. The mechanism through which defoamers operate generally entails minimizing the surface tension of the fluid, permitting bubbles to coalesce and rise to the surface area quicker, where they can then rupture.
Defoamers are formulated from a range of chemical compounds, including organic products, silicones, and surfactants, each customized to specific applications and processes. The choice of defoamer relies on elements such as the kind of product being processed, temperature, and the presence of various other ingredients. Efficient defoamers not just reduce foam development but likewise keep compatibility with the item, making certain that there are no unfavorable results on the final output. Understanding the homes and functions of defoamers is necessary for producers intending to maximize their procedures, boost performance, and keep the honesty of their products.
Secret Advantages of Defoamers
Making use of defoamers in manufacturing processes supplies a series of significant advantages that enhance functional effectiveness and product quality. Among the primary advantages is the reduction of foam formation during production, which can obstruct machinery and interrupt process. By reducing foam, defoamers ensure smoother operations, resulting in reduced downtime and maintenance expenses.
In addition, defoamers boost item uniformity by protecting against air entrapment, which can compromise the honesty of the final product. This is particularly crucial in industries where aesthetic look and structure are essential, such as in paints, layers, and foodstuff. Boosted item high quality not just meets customer expectations however likewise enhances brand name online reputation.
In addition, defoamers can aid in optimizing source usage. By improving the performance of resources use, they add to set you back financial savings and lowered waste, aligning with sustainability goals. Finally, the application of defoamers can lead to shorter handling times, allowing producers to boost manufacturing ability without significant resources investment - defoamers.
Applications in Numerous Industries
In producing processes throughout different industries, the application of defoamers plays a vital duty in boosting efficiency Extra resources and item quality. These chemical ingredients are used in fields such as food and drink, drugs, and textiles to mitigate foam-related challenges.
In the food and beverage market, defoamers are necessary during the fermentation procedure, protecting against frothing that can disrupt manufacturing and spoil the product's stability. In the pharmaceutical market, defoamers are utilized in the formula of fluid medicines, making sure uniformity and security while minimizing waste.
Textile production additionally profits from defoamers, as they are utilized in coloring and completing procedures to advertise also circulation of chemicals and dyes. This application not only enhances the final item's appearance yet also minimizes the quantity of water and energy taken in throughout production.
Additionally, in the paper and pulp industry, defoamers aid keep process performance by reducing foam that can hinder machinery efficiency. In general, the varied applications of defoamers across these industries highlight their significance in optimizing manufacturing procedures and supplying high-grade items.
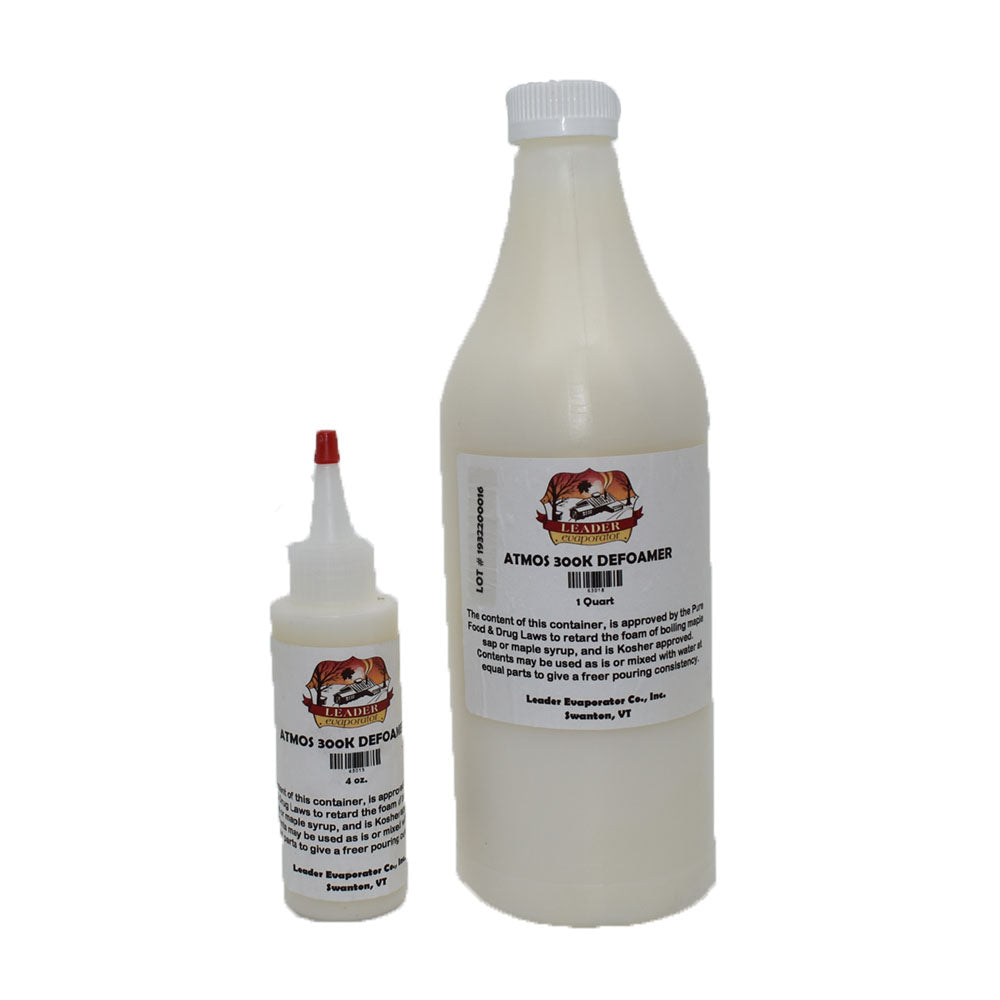
Selecting the Right Defoamer
Selecting an appropriate defoamer is important for making best use of efficiency and high quality in producing procedures. The option of defoamer depends on numerous factors, consisting of the particular application, the kind of foam being generated, and the solution of the item being made.
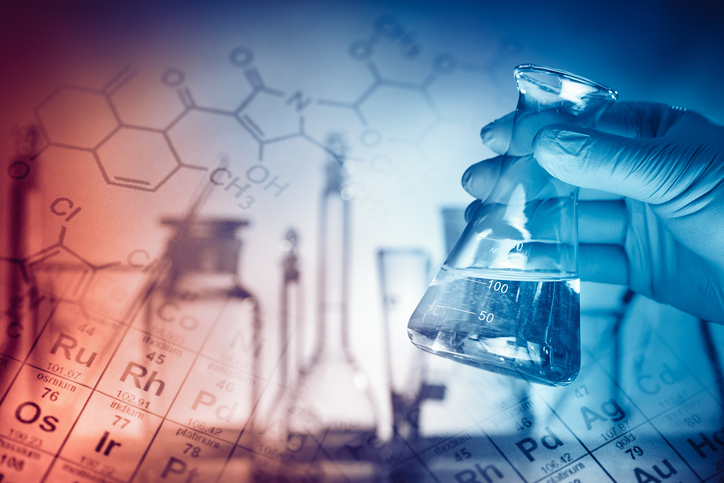
Firstly, consider the chemical compatibility of the defoamer with various other ingredients in your formula. A defoamer that interacts negatively with various other components can detrimentally impact item quality. Furthermore, the temperature level and pH variety throughout handling are essential; some defoamers carry out efficiently under particular problems while ending up being ineffective in others.
Second of all, evaluate the defoamer's performance qualities, such as its capacity to rapidly reduce foam and its perseverance during production. It is vital to choose a product that not just eliminates foam rapidly however also preserves click resources its effectiveness in time.
Finally, consider regulative and environmental factors, especially if your production procedure undergoes strict conformity requirements. Choosing a eco-friendly or low-toxicity defoamer can aid satisfy sustainability goals while making certain operational efficiency. By attentively examining these criteria, makers can make enlightened decisions that boost efficiency and item integrity.
Ideal Practices for Application
Successful execution of defoamers in making processes needs cautious preparation and adherence to ideal techniques. Initially, it's necessary to conduct a detailed evaluation of the manufacturing setting. This includes understanding the details application, the kinds of lathering agents existing, and the operational conditions. Selecting the right defoamer, as previously talked about, is vital; guarantee it is compatible with the materials entailed and addresses the determined lathering concerns efficiently.
Following, maintain clear communication with all stakeholders, including drivers and quality control groups. Training sessions can help ensure that every person comprehends the application treatments, possible influences on product quality, and safety and security factors to consider. Implementing a test phase can additionally be useful; screen performance very closely to gauge efficiency and make necessary adjustments.
Additionally, routine screening and monitoring of foam degrees can offer valuable insights into the defoamer's performance over time. Readjusting does in reaction to modifications in manufacturing variables will certainly aid maintain ideal efficiency - defoamers. Documenting all procedures and results promotes continuous renovation, permitting for fine-tuning of defoamer usage and boosting general efficiency in manufacturing operations.
Verdict
In recap, defoamers play a crucial role in improving performance within manufacturing and production processes. By lessening foam formation and assisting in bubble coalescence, defoamers contribute to boosted item quality, uniformity, and operational performance.
The benefits expand to product high quality and price financial savings, as defoamers aid enhance processes.Defoamers play an important role in numerous manufacturing processes by properly combating the formation of foam, which can disrupt procedures and influence product quality. Comprehending the homes and functions of defoamers is crucial for producers intending to enhance their processes, improve productivity, and preserve the link integrity of their items.
Making use of defoamers in producing procedures supplies a range of considerable advantages that improve functional performance and product quality.In addition, defoamers boost item uniformity by preventing air entrapment, which can endanger the stability of the last item.
Report this page